ZT hat einen neuen geradeverzahnten Primär rausgebracht, mit induktiv gehärteten Zahnflanken.
http://zt-tuning.de/ZT-Kupplungsza…-verzahnt-17-54
Vielleicht will den ja mal jemand testen.
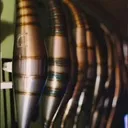
neuer ZT Primär
-
-
...der wird schon ordentlich sein...ZT ist auch ehrlich und empfielt für den harten Eindatz die nadelgelagerten Produkte von Ronge .
-
Cool, find ich auch gut das sie für andere Einsätze Ronge empfehlen.
Das ist jetzt die Konkurrenz zum 70€ MZA Reso Primär
-
...aah ,der Fehlerteufel...empfiehlt und Einsatz ...so wäre es richtig gewesen .
-
Leider hab ich genug gute Serien Primärantriebe für die nächsten Jahre so wenig wie ich fahre sonst hätte ich Lust sofort einen zu bestellen und testen.
-
Das Härteverfahren ist doch meist Induktiv bei derlei Bauteilen.
Wenigstens empfehlen sie Ronge beim Namen.
Nicht so wie SM die Ronge Primäre als Neuheit feiern und Kommentare ob sie denn "Made by Ronge" sind einfach löschen [emoji23]
Gesendet von meinem SM-G925F mit Tapatalk
-
Induktiv härtet man in der Regel nur bei sehr großen Verzahnungen, welche nicht ohne Weiteres durch einen Härteofen passen. Die Bauteile werden normalerweise einsatzgehärtet mit entsprechender Öl oder Gasabschreckung.
Kleinserien gerne auch Vakuumhärten.Beim Induktiven Härten bringst du ringsum nach und nach Wärme ins Bauteil was sich suboptimal auf die Verzüge auswirkt. Diese Verzahnung wird ja hart nicht mehr bearbeitet.
Auf den Bildern bei ZT siehts allerdings so aus als wäre am großen Rad induktiv gehärtet worden. Würd mich mal interessieren wie es kämmt.
Keine Ahnung wie es induktiv mit dem Einsatz funktioniert? Müsste dann unter einer entsprechenden Endogasatmosphäre (Gasaufkohlung) gehärtet werden wobei die Verweildauer in der Atmosphäre aber viel zu kurz wäre.Gruß Michel
-
Induktiv härtet man in der Regel nur bei sehr großen Verzahnungen, welche nicht ohne Weiteres durch einen Härteofen passen.Jupp, induktive Härtung hab ich mir mal in der Kugeldrehkranzfertigung bei Liebherr anschauen dürfen. Durchmesser der Zahnkränze so von 1m bis 5m
Keine Ahnung wie es induktiv mit dem Einsatz funktioniert? Müsste dann unter einer entsprechenden Endogasatmosphäre (Gasaufkohlung) gehärtet werden wobei die Verweildauer in der Atmosphäre aber viel zu kurz wäre.Ich versteh nur Bahnhof. Kannst du das bitte mal für einen normalsterblichen übersetzen?
-
Beim Einsatzstahl wird ein Stahl gewählt, welcher einen so niedrigen Kohlestoffgehalt hat, dass er nicht durchhärtet. Deshalb musst du die Randschicht aufkohlen. Außen Fest, innen zäh.
Da du zum Härten einen gewissen Kohlestoffgehalt brauchst, wird die Randschicht beim Härten entsprechend angereichert. Das geschieht entweder im Einsatzkasten oder unter einer Gasatmosphäre.
In der Regel dringt die Kohlestoffanreicherung pro Stunde 0,1mm in die Oberfläche ein. Bei Modul 2 beträgt die gewünschte Einsatztiefe i.d.R. ca. 0,5 - 1mm.Bei mega großen Zahnrädern kannst du einen Stahl mit hohem Kohlestoffanteil nehmen, da durch die Induktion nur die äußere Schicht auf Härtetemperatur gebracht wird, das Teil bleibt innen weich.
Auf den Bildern bei ZT ist die Verzahnung bis unter den Zahnfuß auf Temperatur gebracht, somit müssten alle Zähne durchgehärtet sein. Bin aber auch nicht der Verfahrenstechnikerprofi... -
Danke für die Erklärung!
-
Wenn die Zahnräder durchgehärtet sind steht sich mir die Frage der Restelastizität. Sollte diese zu gering sein könnten die Zähne ausbrechen. Ist sind die bedenken nicht gegründet?
-
Das Bauteil ist klein genug um es auf 360° mit einmal zu härten.
Solch induktor zu bauen ist kein Problem.
Induktiv ist für mich nur suboptimal.. nun ja wir wollen Jens hier ja nicht den Spaß nehmen selbst zu entwickeln und ihm alle Tips zuspielen...
Ich geh jedenfalls davon aus das die Härtung nicht so ist, wie es sich jemand mit Anspruch wünscht.
Das ist eher der Placeboeffekt für einige Leute was "gehärtetes" zu haben...
Wie die Verzahnung dann ineinander kämt wird sich zeigen. -
.....
Induktiv ist für mich nur suboptimal.. nun ja wir wollen Jens hier ja nicht den Spaß nehmen selbst zu entwickeln und ihm alle Tips zuspielen...Ich weis nicht ob ich kotzen oder lachen soll....
Auszug:
".....Vor allem bei der Produktion von Zahnrädern und Wellen, als zentrale Bauteile von Antrieb, Getriebe und Motor, sind kürzeste Taktzeiten gefordert und werden von den Fertigungsmaschinen der neuesten Generation auch erreicht. Doch wie lassen sich die Anforderungen im Härteprozess umsetzen? Die Antwort: Induktives Härten.
Die klassische Form des Härtens ist das Einsatzhärten, bei dem das komplette Werkstück über Stunden erwärmt werden muss um die Härtung zu erreichen. Gerade für die industrielle Fertigung von Zahnrädern, hat diese Form des Härtens viele Nachteile, wie z.B. der hohe Energie- und Zeitaufwand, so dass sich in den letzten Jahren vor allem das induktive Härten als technologische Alternative entwickelt hat. Beim induktiven Randschichthärten geschieht die Wärmeeinbringung mittels Induktion von Wirbelströmen in das Werkstück. Der besondere Clou ist dabei, dass nur die Bereiche erwärmt werden, die tatsächlich gehärtet werden müssen, der Rest des Bauteils bleibt von der Wärme unbeeinflusst. Dies geschieht aufgrund von 2 wichtigen Mechanismen: Durch die exakte Steuerung der Frequenz mit der die Wirbelströme eingebracht werden, wird nur ein kleiner Randbereich von wenigen Millimetern Tiefe erhitzt. Das wiederum führt dazu, dass der gesamte Erwärmungsprozess weniger als 0,5 Sekunden betragen kann, viel zu kurz um eine thermische Beeinflussung des gesamten Werkstücks zu ermöglichen.............."
Quelle: http://www.eldec.net/de/unternehmen…produktion.html
Das Induktionshärten oder auch Randschichthärten bietet eine optimale Möglichkeit, Bauteile lediglich in Teilbereichen zu härten (partielles Härten). Hierbei werden die zu härtenden Bereiche mit Hilfe eines Induktors durch Induktionsstrom partiell über eine gewisse Zeit erhitzt. Die Abschreckung erfolgt durch eine Wasserbrause direkt im Anschluss, kann aber gegebenenfalls auch entfallen.
Es handelt sich hierbei um ein äußerst präzises Verfahren, welches sich sehr genau steuern lässt um die gewünschte Härte in der Randschicht des Bauteils zu erreichen.
Dieses Verfahren wird häufig im Werkzeugbau eingesetzt und bietet neben der Erhöhung der Verschleißfestigkeit den Vorteil, exakt definierte Teilbereiche mit einer verbesserten mechanischen Bauteileigenschaften, wie z.B. einer höheren Kerbschlagfestigkeit zu versehen.
Geeignete Werkstoffe:
Vergütungsstähle mit einem Kohlenstoffgehalt von mehr als 0,3%
Vorteile des Verfahrens:
Steigerung der Härte in der Randschicht bei gleichzeitig zähem Kern
Erhöhte Verschleißbeständigkeit
Erhöhte Biegewechselfestigkeit
geringer Verzug -
Ich weis nicht ob ich kotzen oder lachen ....
Mache was du möchtest...Im Gegensatz zu dir härte ich auch in der Praxis bei mir in der Firma Induktiv. Großverzahnungen werden auch induktiv gehärtet.
Da ist der induktor aber schon größer als ein Kupplungskorb.
Nur weil du es theoretisch mal irgendwo gelesen hast muss es nicht so sein. Groß auf klein ist nicht 1:1 zu projektzieren bzw runterzuskalieren.
Theoretisch hast du schon viele super Sachen angeboten wo du dich super informiert hast. Praktisch war es dann einfach nicht haltbar. Das ist keine üble Nachrede. Das ist nur ein realer Auszug aus dem was hier an Feedback kam, das "Man(n)" hier im Forum im einzelnen Nachlesen kann.
Wir werden sehen was dein Zeug hält, nicht ohne Grund wird dort stehen das man lieber zum Ronge Kk greifen soll.... klingt wie eine Ausrede wenn's kaputt ist.. ich hab euch ja gesagt nehmt lieber was anderes.
Noch schlimmer ist das du null% Kritikfähig bist. Brauchst auch nicht wieder weinent zum admin laufen das der Beitrag gelöscht werden soll. Schließlich steht nur wahres drin und beleidigt wird auch niemand. Steh einfach mal dazu, wie du dich gibst.
Du könntest auch gerne mal ein Härteprotokoll der Verfahrensprobe mit anhängen.Wenn es hält ist es gut. Ich möchte mich erst überzeugen lassen.
Wie hart und ist die Randschicht und wie dick!Gruss
-
Interessant dass du in der Praxis dieses "suboptimales" Härteverfahren verwendest.
Wenn es doch quasi laut deiner Aussage kein Verfahren ist, wo meine eine Härtung erreicht, wie es sich jemand mit Anspruch wünscht.Haben eure Kunden keinen Anspruch?
Wir haben zusammen mit den Hersteller verschiedene Wege diskutiert und auch getestet und konnten mit diesen Verfahren die besten Ergebnisse erzielen, gerade weil der Fuß nicht durchhärtet und weil der Verzug extrem gering ist.
Dass ich dann angepisst bin, wenn ich hier schon wieder lesen darf:
1. Wie sehr doch die Verzahnung kämmt
2. Dass Ja quasi das ganze Zahnrad verzogen sein muss
3. Dass die Zähne ja komplett durchgehärtet sein müssen.Ohne das jemand von euch Experten das Teil in der Hand gehabt wird, sollte wohl doch ein kleines bisschen Nachvollziehbar sein.
Gegen konstruktive Kritik habe ich gar nichts.
Nur unter konstruktiv verstehe ich nicht wenn Ihr anhand von 2-3 Fotos aus der Wurstsuppe irgendwas zusammenreimt.
-
Wir härten keine kleine Verzahnung. Darauf ist meine Aussage bezogen.
Das es geht weiß ich, auch kleine Verzahnung. Ich kenne auch die kosten dafür. Daher geh ich nicht von optimal aus...
Bitte richtig lesen!
Von in der Hand halten weiß ich auch nicht ob es so gehärtet ist wie es sich gehört... du experte. -
Wir härten in der Großserienfertigung im Durchstossofen. Induktiv wäre bei all den gehärteten Funktionsflächen an den Getriebebauteilen nicht möglich. Das Durchstoßen dauert ca 8 - 10h. Die Öfen sind entsprechend lang.
Ausreichend für 300.000 Getriebe im Jahr x die Anzahl der Bauteile. Kostenmäßig gehts im Grundrauschen unter, da sind andere Prozesse teurer. Induktiv härten wir Nockenwellen und Kurbelwellen.
Dort machts Sinn. Spass mit Verzügen haben wir bei den großen schlanken Ringrädern. Bei unserem älteren Getriebe wird sogar die Mikrogeometrie weich geschabt und Verzüge vorgehalten. Alle Verzüge werden von Experten berechnet und in der Werkzeugschleiferei ins Werkzeug gebracht. Da sprechen wir von Toleranzen im einstelligen µm-Bereich. Das sind meine Erfahrungen aus der Praxis.Wollt damit auch keine riesen Diskussion anstoßen und deshalb hab ich auch geschrieben, dass ich kein Verfahrenstrechikprofi bin, dafür haben wir die entsprechednen Experten im Haus.
Entscheidend ist das was am Ende bei raus kommt. Wie man das Ziel erreicht ist total Wurst. Wenns funktioniert, dann ists doch gut.
Die Qualitätsansprüche an einen Simsonprimär sind gegenüber dem was im Automotivebereich gemacht wird, sehr gering.
Die Teile werden fertiggefräst, besitzen keine Mikrogeometrie usw.Also weitermachen.
-
Wir härten in der Großserienfertigung im Durchstossofen. Induktiv wäre bei all den gehärteten Funktionsflächen an den Getriebebauteilen nicht möglich. Das Durchstoßen dauert ca 8 - 10h. Die Öfen sind entsprechend lang.
Ausreichend für 300.000 Getriebe im Jahr x die Anzahl der Bauteile. Kostenmäßig gehts im Grundrauschen unter, da sind andere Prozesse teurer. Induktiv härten wir Nockenwellen und Kurbelwellen.
Dort machts Sinn. Spass mit Verzügen haben wir bei den großen schlanken Ringrädern. Bei unserem älteren Getriebe wird sogar die Mikrogeometrie weich geschabt und Verzüge vorgehalten. Alle Verzüge werden von Experten berechnet und in der Werkzeugschleiferei ins Werkzeug gebracht. Da sprechen wir von Toleranzen im einstelligen µm-Bereich. Das sind meine Erfahrungen aus der Praxis.Wollt damit auch keine riesen Diskussion anstoßen und deshalb hab ich auch geschrieben, dass ich kein Verfahrenstrechikprofi bin, dafür haben wir die entsprechednen Experten im Haus.
Entscheidend ist das was am Ende bei raus kommt. Wie man das Ziel erreicht ist total Wurst. Wenns funktioniert, dann ists doch gut.
Die Qualitätsansprüche an einen Simsonprimär sind gegenüber dem was im Automotivebereich gemacht wird, sehr gering.
Die Teile werden fertiggefräst, besitzen keine Mikrogeometrie usw.Also weitermachen.
-
Entscheidend ist das was am Ende bei raus kommt. Wie man das Ziel erreicht ist total Wurst. Wenns funktioniert, dann ists doch gut.Bravo! Das ist genau meine Meinung. Wenns hält und funktioniert dann hat ZT alles richtig gemacht und wir können uns über eine weitere Alternative bei den Primärantrieben freuen!
Erstmal abwarten bzw. noch besser : selber testen. -
...ich persönlich freue mich über jede Neuerung ,die den Markt belebt und die Marke Simson weiter am Leben erhält .
-
Jetzt mitmachen!
Sie haben noch kein Benutzerkonto auf unserer Seite? Registrieren Sie sich kostenlos und nehmen Sie an unserer Community teil!